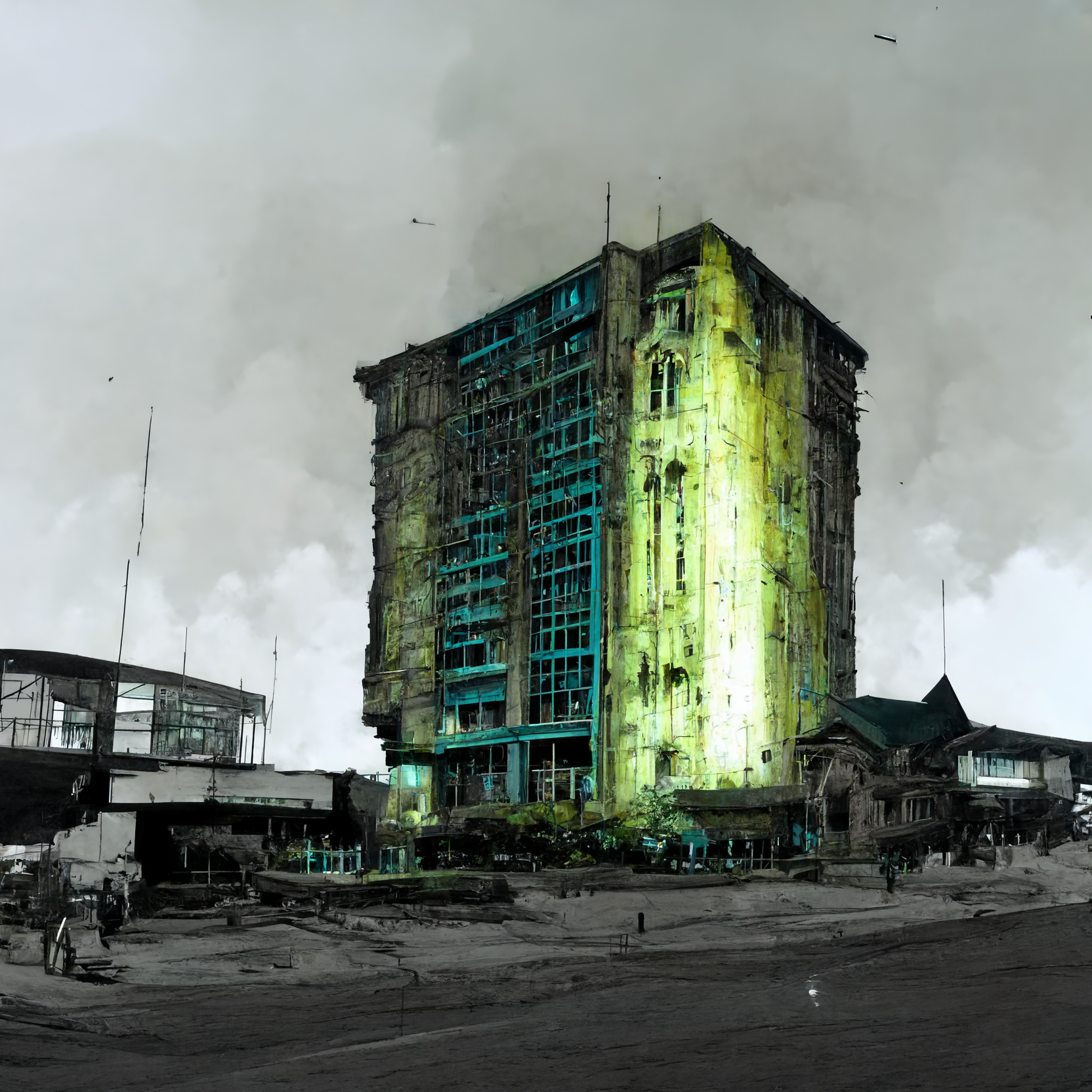
Robotic ImagingJanuary 9, 2023
If you work in the Architecture, Engineering, or Construction (AEC) industry, then you know that time is money. And if there's one technology that can save you time and money, it's 3D laser scanning. With 3D laser scanning, you can create precise as-built models of existing structures quickly and easily. This technology can also be used to create highly accurate point clouds that can be used for a variety of purposes, such as component recognition, facilities management, quantity takeoffs, and clash detection.
In short, everyone in the AEC industry would significantly benefit from laser scanning technology. But what exactly is 3D laser scanning? And how does it work? Keep reading to find out.
How Does 3D Laser Scanning Work?
3D laser scanning, also known as LiDAR (Light Detection and Ranging), is a remote sensing technology that uses laser pulses to measure distance. By firing millions of laser pulses per second at a target and measuring the time it takes for each pulse to bounce back, a 3D scanner can create a highly accurate point cloud representation of the target. This point cloud can then be exported to various CAD software programs, where it can be used to create as-built models or for other purposes.
Benefits of 3D Laser Scanning
There are many benefits of using 3D laser scanning over traditional surveying methods, such as total station surveying. First and foremost, 3D laser scanning is much faster than traditional surveying methods. A single scanner can collect up to 1 million points per second, which means that large projects can be scanned in a matter of hours instead of days or weeks. Furthermore, because the data is collected electronically, there's no need to worry about paper surveys getting lost or damaged. Finally, 3D laser scanners are highly portable and easy to use, which means that they can be used in a variety of settings, both indoors and outdoors.
Photogrammetry vs LiDAR
So now that you know what 3D laser scanning is and how it works, you may be wondering how it compares to other measurement technologies, such as photogrammetry. In short, photogrammetry is an indirect measurement method that uses photos to calculate measurements. This method is typically used for larger projects where accuracy is less important. On the other hand, LiDAR is a direct measurement method that uses lasers to directly measure distance. This method is more accurate than photogrammetry but typically costs more money. The table below provides a more detailed comparison of these two measurement methods:
Method | Accuracy | Speed | Cost |
---|---|---|---|
Photogrammetry | 9mm | Fast | $0.10 - $0.50 / sqft* |
LiDAR | 2mm | Slower | $0.50 - $1.00 / sqft* |
*Prices vary based on project size, deliverables and building typology. These prices are for 2D CAD drawing production only. Contact us for a free quote!
As you can see from the table above, LiDAR is more accurate but also more expensive than photogrammetry. While photogrammetry is fast and relatively cheap, it's not as accurate as LiDAR. On the other hand, while LiDAR is slower and more expensive than photogrammetry, it's much more accurate.
So which method should you use? Ultimately, the decision comes down to your project requirements. If accuracy is your top priority and cost is not an issue, then LiDAR is the way to go. However, if speed and cost are your top priorities and accuracy is not as important, then photogrammetry may be the better option.
In conclusion, everyone in the AEC industry would significantly benefit from using 3D laser scanning technology due to its many advantages over traditional surveying methods.If you're looking for a fast and easy way to create precise as-built models or point clouds for facilities management clash detection, or quantity takeoffs, then look no further than 3D laser scanning!